How a British company launched a green, clean hybrid rocket engine
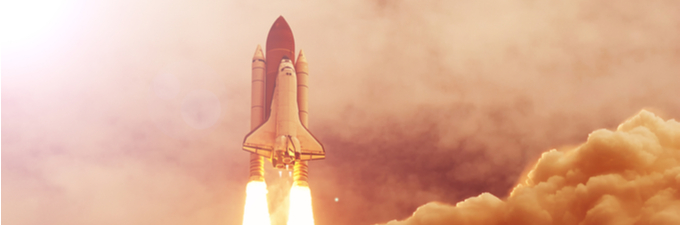
August 2021: a team of rocket scientists, engineers and physicists from British company Pulsar Fusion sit round a table in the Caribbean discussing hybrid rocket engines and the US-dominated space sector. What would it take for a UK company to design and build a green, clean hybrid rocket engine in order to demonstrate UK proficiency and capability?
“The British government wants 20 per cent in the space sector, but it’s difficult to see how that can happen if we’re not actually building space technology in the UK,” says CEO Richard Dinan. “No one builds this stuff in the UK and Europe – there isn’t the investment. There are a lot of companies with intentions to do so, but fewer have actually built and demonstrated their technology. We genuinely feel there is a commercial application for reliable, relatively cheap clean rocket engines built outside of US regulation in the UK.
“We had the budget and the investment and we wanted to be the company that did it.”
Project lift-off
By November – barely four months later – the team had built two hybrid rocket engines from their Bletchley base and demonstrated the technology in both the UK and Switzerland.
The hybrid rocket engine burns two fuels simultaneously: high-density polyethylene (HDPE) made from recycled plastic and nitrous oxide, which together produce a non-toxic, water-based plume that is literally vapourised.
All in all, it was an incredible feat, especially during a pandemic. So how did they do it?
According to Dinan, it was a combination of extreme multitasking, exceptional logistics efficiency and having a highly talented and motivated team on board.
“We built and assembled everything ourselves at our Bletchley site,” Dinan explains. “We hired really good rocket engineers and physicists. And we did everything simultaneously: testing, prototyping, control testing, checking safety systems and carrying out structural tests. We even built the feed systems ourselves, ensuring they were portable enough to transport internationally.”
Even navigating various supply chains during a time when most other industries were experiencing massive delays and increased costs did not pose a problem.
“A lot of the time, it’s harder to order two parts than 100,000, so you usually need to order more than you need and be prepared to overpay. We were paying vastly over the odds in some cases and we over-ordered many components to ensure they arrived on time. I was determined I wasn’t going to wait a year for one particular part – the whole industry moves on in a year.”
Spares too were purchased, even if they weren’t necessarily needed. “Having a spare of anything up to £10,000 is actually much cheaper than the alternative: if something breaks while on location after you’ve already flown everyone over, paid for flights and hotels, you then need to return home while you wait for a replacement and then rearrange the whole thing again.”
Standing on the shoulders of a century of research
Ultimately, Dinan insists, it was the entire team who ensured the ultimate success of their project: everyone involved, including couriers and cleaners did over and above their job description and, in some cases, worked for free. Even the test sites themselves, COTEC in Salisbury and Gstaad airport in Switzerland, supported Pulsar with risk assessments, senior staff time and high-level clearances, all of which made these pioneering tests possible.
“We were standing on the shoulders of probably a century of research,” says Dinan. “We had so much support from the team as well as international and government support. Without that, it would not have been possible.”
Even so, there was a huge list of things to consider and plan for from both a safety and logistical point of view. Previous demonstrations had taken place in controlled environments in their test centres, but carrying out tests in the field was a different ball game, from putting in place safety procedures and checks around high pressure gas and transporting it, to dealing with different regulations in different countries.
The demonstrations themselves went more or less according to plan, despite the blizzard that hit during the second round of testing in Switzerland.
“We were surrounded by mountains and it was beautifully scenic. It was an unbelievable place for a rocket engine to be tested. We sat inside bunkers with camera screens with very powerful cameras to watch what was happening in front of the engine and had a 30-second countdown to show the launch, then a five-second countdown before the engine was hit with liquid nitrous oxide at full pressure, which was amazing to watch. It was stunningly loud so our microphones couldn’t pick it up.”
The flame was seven metres long and exhaust engine speeds were recorded at Mach 7, capable of launching a small rocket well above UK airspace.
One giant leap?
Dinan and the team believe this project will have ‘massive’ implications for the UK space sector and themselves as a company. “Any company wanting this tech is having to rely on America, but we’ve proved it doesn’t have to be this way,” says Dinan.
In fact, Pulsar Fusion have their eyes on bigger, even larger feats: using nuclear fusion technologies to enable interplanetary travel.
“We’ve been working on these technologies for nine years,” Dinan explains. “Nuclear fusion can produce hyper exhaust speeds, which have the potential to enable meaningful distances into space. We’re wanting to open peoples’ minds to the fact that we may – one day – leave our solar system, four light years away. It can open up a very weird world.”
You may also be interested in
0 comments
Log in to post a comment, or create an account if you don't have one already.