How we kept our construction project going during national lockdowns
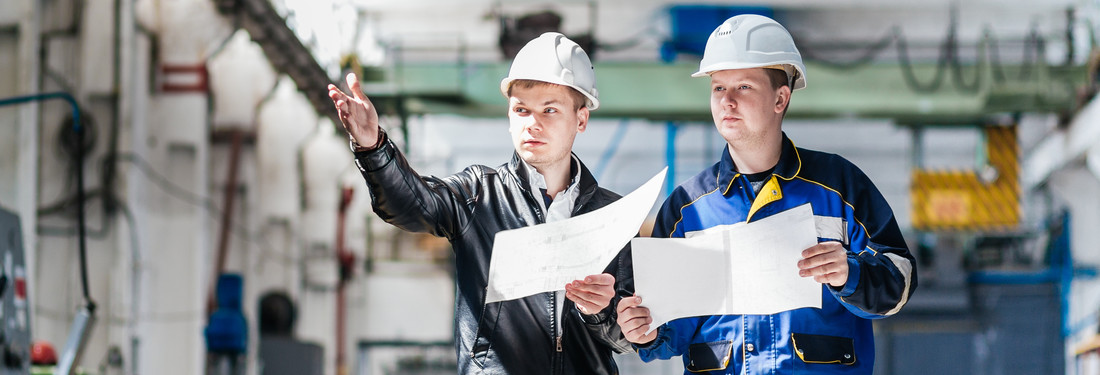
As lockdowns continue to ease and we see some sort of 2019 normality, we look back at how tech changed the way we worked over the last few years. The North London Heat and Power Project (NLHPP) is replacing the existing waste management plant that has served north London well for nearly 50 years and has diverted more than 21 million tonnes of non-recyclable waste, which would otherwise have gone to landfill. This is a major sustainable project and has over 150 employees working onsite.
When COVID-19 struck, we needed to find new and innovative ways to protect our staff while keeping the project on schedule. The Beable tracker was implemented on the project; a wearable device that tracks and monitors proximity, and alerts individuals when they’re closer than two metres. This device ensured that we maintained the recommended social distancing guidelines, to help prevent the spread of the COVID-19 virus onsite and could keep the project going.
The pandemic resulted in a nationwide lockdown that prohibited a large proportion of the workforce from going to their place of work, creating uncertainty and fear, especially for workers that couldn’t work from home. Particularly within the construction industry, a lot of workers felt excluded from the protection of a lockdown as their sites weren’t closed. They still had to go to work despite not having adequate safety measures in place creating a huge sense of risk amongst workers.
The NLHPP is a large project in the public sector with a diverse workforce, ranging from office workers to security staff and construction workers working in close proximity to deliver a waste management facility that local communities can take pride in. Although we were focused on the continuation of the works and limiting the cost and time disruption of the pandemic, our number one priority was the health, safety and wellbeing of our staff. The unprecedented pandemic led us to find a solution to our problem and mitigate the biggest project risk through new ideas and innovations.
We considered a number of solutions, including rescheduling works to allow for social distancing, redesigning site protocols and procedures, additional PPE, as well as testing a one-way system in areas of the site. Though it helped, we needed additional measures to ensure the welfare of our personnel. This is where new technology and data helped our project stay on track, keeping the teams onsite safe and secure.
The idea of wearable tech came about when Stuart Humphries, the construction assurance manager for the NLHPP, attended an industry event and spotted the Moonbeam device. The Moonbeam is a bracelet that tracks and monitors an individual’s stress levels and flags this information to senior management. The tool was a great asset to monitor wellbeing and added an extra safety level for lone workers.
Upon further research, a similar wearable device called the Beable tracker was discovered. Onsite personnel are equipped with a personal bracelet/lanyard which monitors and records their location onsite and alerts them when they are within two metres of another onsite member of staff, encouraging social distancing. Onsite personnel also complete a survey at the start of each day, the outcome being one of the following results: get a COVID-19 test, stay home and isolate, speak to manager, freely go to work, etc. As the bracelets/lanyards monitor and record onsite personnel locations, if a member of staff tests positive for COVID-19, all those who have been within two metres with that member of staff will be notified.
By issuing Beable devices to the onsite workforce, it provides all with the peace of mind that we are doing everything we can to protect our workforce. The system reduces the risk of human error and utilises data management, monitoring of work patterns and social distancing reminders to ensure the project went ahead as scheduled, whilst reducing the risk of viral transmission.
Looking at the metrics and data from the results of working on site, we were able to successfully manage the number of proximity breaches with notable numbers of alerts being decreased. In addition to the use of the Beable device, these positive results were supported by logistical changes including staggering shift times and patterns to enable less interaction during peak points of the day, and weekly COVID testing.
The quick and efficient thinking of project leaders and investment in new tech, helped ensure that we were able to keep the project going, control the spread of COVID-19 onsite and comply with the government social distancing rules. The Beable tracker also enabled an additional line of defence and assisted with the track and trace initiative at a local level resulting in no significant outbreaks of COVID-19 on the North London Heat and Power Project.
You may also be interested in:
- Coronavirus diaries: Two tales of tech project managers adapting to the crisis
- Listening to the APM Podcast
- Joining the APM community as a member for exclusive articles
This blog was co-written by Stuart Humphries and Emmanuela Ntinugwa
Emmanuela is a Graduate Project Manager at Arup. Currently working on the North London Heat and power project with the Continuous Improvement and Innovation team and with the Project delivery team.
0 comments
Log in to post a comment, or create an account if you don't have one already.