Implementing vapour recovery solutions at Aramco bulk plants
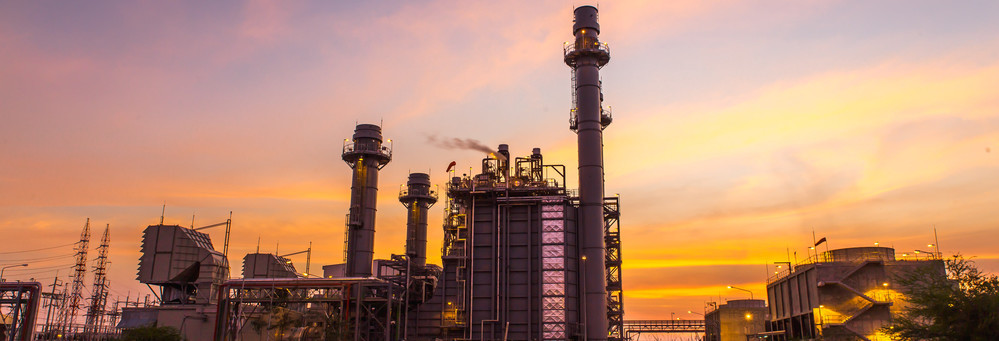
A Saudi Aramco (Aramco) project management team have successfully concluded the implementation of the Vapour Recovery Systems at the major domestic refined product distribution bulk plants in Saudi Arabia. The aim was to handle vapours that are emitted directly into the atmosphere during truck loading processes.
This is the first phase of a two phase program that is planned to have similar systems installed at all remaining bulk plants in Saudi Arabia. This major milestone highlights the importance of environmental project management as well as the organisation’s compliance to ensure facilities become more environmentally friendly.
1. Environment protection challenge
Previously, vapour emissions during the truck loading processes went directly into the atmosphere through a vent stack located above the loading bay canopies. These light-end vapours, also known as volatile organic compounds (VOC) are discharged into the atmosphere and contribute to the low-level ozone formation in the surrounding area when reacting with sunlight. Exposure to VOCs have been attributed with respiratory as well as eye, nose and throat irritations in addition to harming plantation and the environment near the venting source.
2. Product recovery
In addition to the environmental protection imperatives to recover the hydrocarbon vapours, it was logical to conserve product. This benefit means that the vapours can be processed through a vapour recovery unit to be enriched via activated carbon beds, back to the liquid state and reintroduced into the fill lines of the truck loading stations. In essence, that means converting vapours that would normally be lost to the surrounding atmosphere into recovered and utilised product.
The average refined product recovery rate for the vapour recovery system is approximately 1-1.2 barrels recovered for every 1000 barrels loaded. As per latest projections for product production at the current bulk plants where the units are already installed, we are looking at a potential recovery of 641 barrels a day of gasoline.
3. Project implementation
The implementation of this new technology at Aramco distribution plants faced some expected resistance especially from the plant operators. They had doubts whether the unit would achieve its expected benefits and concerns whether the system would be easy to run and maintain.
The project team anticipated this risk early on the project and have put in place actions to address it. Most importantly, the team ensured two-way communication with the operations facility staff during the design phase to work directly with the technology owners and raise their concerns. In addition, operators were invited to participate in factory acceptance testing to witness the test of the units before it was installed at their facility. Furthermore, the project team invited operators to attend the start-up of the vapour recovery unit to ensure their buy-in to the integrity of the system and prove that it can realise its benefits. Stakeholder engagement and involvement has been vital to delivery and the benefits of the project.
4. Future implementation plan
Following the successful completion of phase one, Aramco is planning to implement the same at the remaining bulk plants in phase two.
Vapour recovery units have been proven to be a viable solution to furthering domestic and international environmental emission directives and regulations. Moreover, this shows Aramco’s adherence to internal corporate values relating to safety, health and environmental protection. Several related initiatives are being implemented throughout Saudi Arabia via projects directly targeted at improvement of the wellbeing of its community and environment, in particular, air quality.
These projects lead to improved quality of life and further align to worldwide objectives for a ‘greener’ and sustainable planet. It’s vital for organisations and projects to look at systems and address how things can be improved as the climate crisis rages on – we need innovative solutions and who better to be at the heart of this than project professionals.
With thanks to Mohammad A Jumaia, Abdulrahim A Hazmi and Sami H Najrani.
You may also be interested in:
0 comments
Log in to post a comment, or create an account if you don't have one already.